Preparing Fuselage
to Accept the Horizontal Stabilizer
Installing the horizontal stabilizer to the fuselage is an exciting
milestone. The boat will really begin to look like an airplane.
However, actually bonding the horizontal stab to the fuse is the
easy part. First we have to prepare the fuselage to accept
it--this will be accomplished in the following
steps:
- Level the fuselage.
- Mark the location of the rear bulkhead and the rear of the horizontal
stab on the fuselage.
- Trim top of rear fuselage to accept horizontal stabilizer.
- Fabricate and Install rear bulkhead.
- Postcure rear fuselage interior.
Step 1 – Level the Fuselage. The first step is to level
up the fuselage. You should have a technique developed for
this operation by this point. I use the lines we drew on the
firewall to define in the roll axis of the fuselage and I use lines
I have marked down the side of the fuselage to define the pitch axis. These
lines were added when we bonded the fuselage halves together. Further
I bonded a couple of ‘line levels’ to the fuselage to
make it quick and easy to re-level the assembly. These are
little levels that are intended to be hung on a string that I hot
glued to several locations on the fuselage. They are quite
effective.
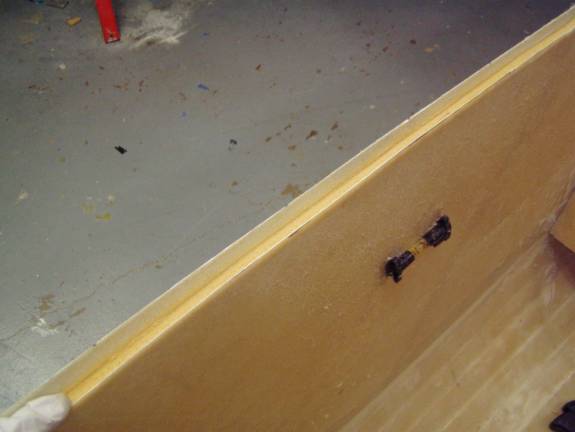
Line Level Bonded on Fuselage Side for Pitch Axis Level
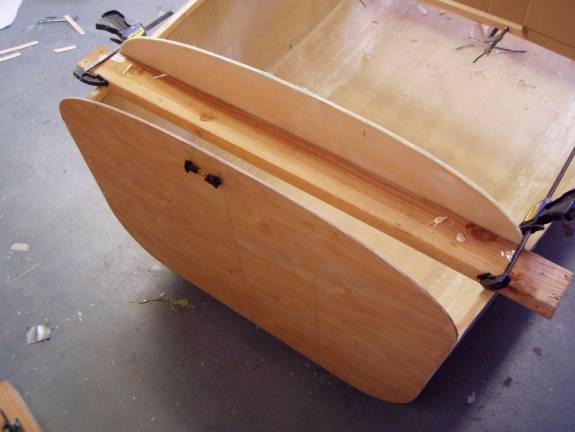
Line Level Bonded on Firewall for Roll Axis Level
Step 1 – Locate Horizontal Stab Position. Once the
fuselage is level we need to locate a couple of key locations on
the fuselage; the location of the horizontal stabilizer and the location
of the rear bulkhead. The rear edge of the horizontal stabilizer
is located at 169 7/8” from the firewall and the front side
of the rear bulkhead is located 155” from the firewall. When
measuring these distances it is important to stabilize the firewall. A
good way to do this is will a 2X4 clamped to it in a similar manner
to the way a 2X4 is clamped to the bulkhead in the above photo. If
you do not stabilize the firewall you will notice that it will flex
aft as you pull your tape measure tight. You want an accurate
and repeatable measurement to these two critical points.
Step 2 – Print Template. Print the two rear fuselage
template sheets (Sheet1 and Sheet2) and tape them together to create
the full size sheet as shown below. Cut out the fuselage portion. This
is a special template created from a view normal to the fuselage
side, not to the centerline of the aircraft. That is, the dimensions
only make sense once the template is taped to the side of the fuselage.

Full Size Rear Fuselage Template Sheet
Step 3 – Tape Template to Fuselage Side – Affix
the template to the side of the fuselage as shown below using the
location of the rear side of the horizontal stabilizer and the level
line. The level line marked on the template should be level
with the horizontal line on the firewall. Use your laser level
to align this as in the photo below. Re-level the fuselage
if needed to get the template to be positioned as shown. If
you do need to re-level to get the template to be placed properly,
reset your permanently placed line levels as we will be precisely
adjusting the horizontal stabilizer incidence angle in the process
and the rest of the construction will be referenced to the level
line we define now.
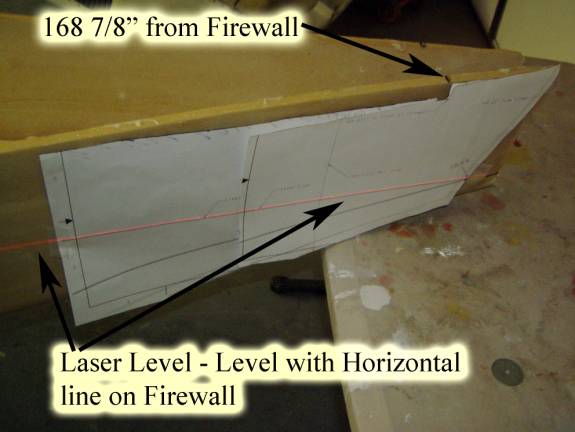
Proper Position of Template
Step 4 – Mark Horizontal Stab Position – Mark the material
to be removed from the fuselage side as shown below. Also mark
the rear section of the fuselage to be removed for the vertical stabilizer. This
step is not shown in the accompanying photographs, but this is the
best time to do this.
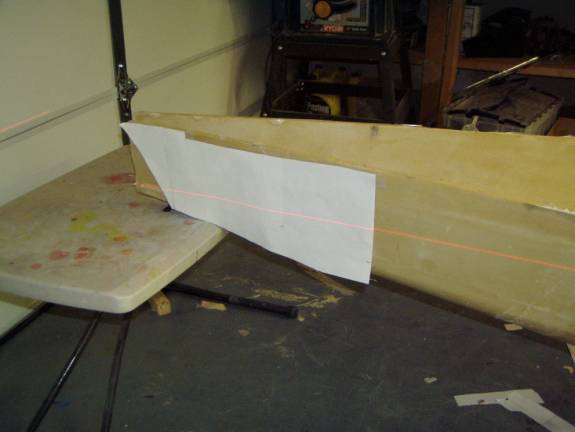
Template positioned on Co-Pilot side of fuselage
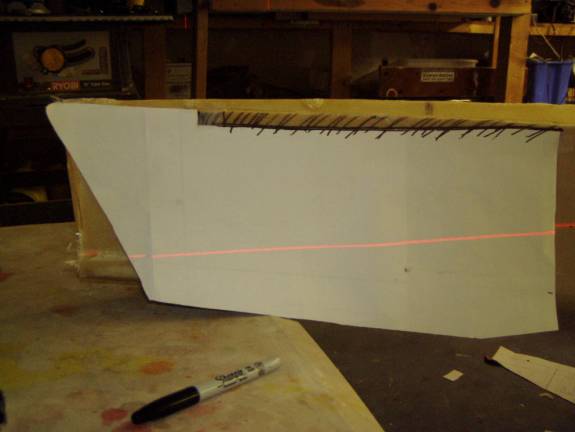
Mark Material to be Removed for Horizontal Stab
Step 5 – Remove material from fuselage to create shelf
for Horizontal Stab – Remove the material that was marked
in the previous step. Also remove the material aft of the
template as this is for the vertical stab. This step is
not shown in the photos, but should be done now.
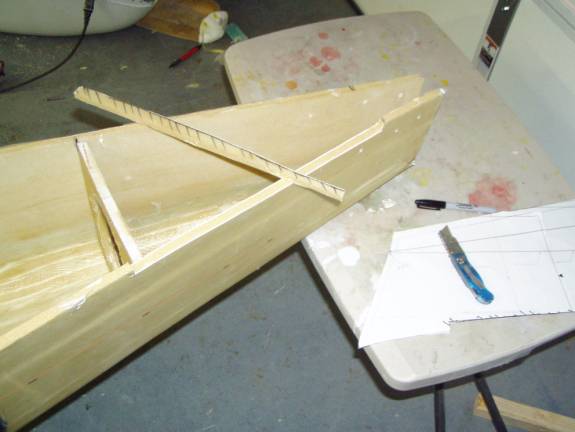
Remove Material
Step 6 – Fabricate Rear Bulkhead – Print out
the full size template
for the rear bulkhead and cut out a bulkhead
from ½” thick 4.5lb. last-a-foam. Cut out the center
section and radius the edges of the center hole. Notice that
the large hole in the center has small ears cut out near the bottom,
these are to provide additional clearance for the rudder cables and
are not reflected in the bulkhead in the photos (yet). Layup
a one layer BID on each side of the bulkhead, smoothing the glass
around the radius in the center hole. I will not detail how
to do this as you are an expert at fiberglass layups by now (vacuum,
slurry, etc.).
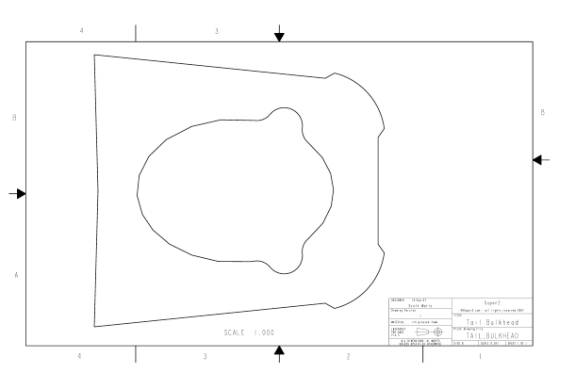
Rear Bulkhead Template
Step 7 – Position Rear Bulkhead – Position the rear
bulkhead as shown in the following two photos. You will need to trim
the bulkhead so it tapers to the rear in order to get a good fit
with the fuselage sides. Its position is defined by three constraints: (1.)
its forward edge is 155 inches from the front of the firewall. This
was marked in an earlier step on the fuselage. (2.) Its top
rests against the bottom of the horizontal stabilizer while it is
sitting on the fuselage. (3.) It is level vertically-use a
small carpenters level to insure this. Once it is properly positioned,
draw a line along the front edge onto the fuselage and make a couple
of alignment marks as shown to allow you to position it correctly.
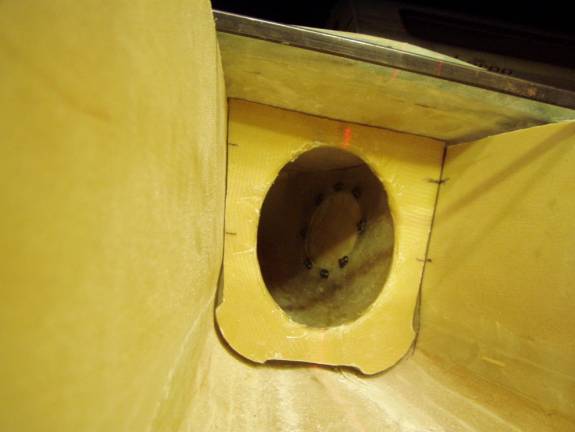
RearBulkhead in proper position against Horizontal Stab
If required, use a clamp as shown below to pull the fuselage sides
in against the bulkhead.
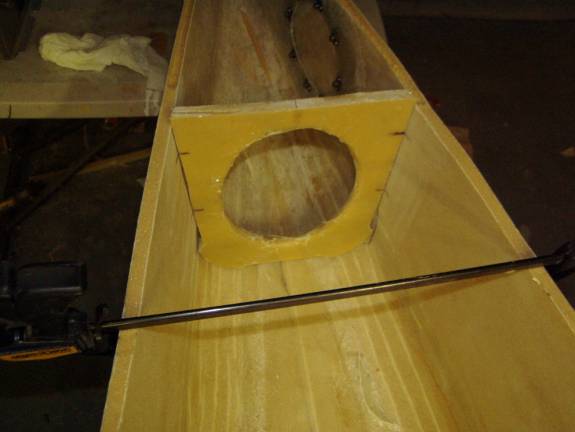
Bulkhead properly positioned and clamped.
Step 8 – Bond Rear Fuselage in Place – Once the rear
bulkhead is positioned properly, bond it into place. Use thick
micro to create a radius and fill all gaps between it and the fuselage. Then
layup a two BID strip of fiberglass on both sides of the bulkhead/fuselage
joint, insuring the overlap is at least and inch and a half on both
sides. Let cure.
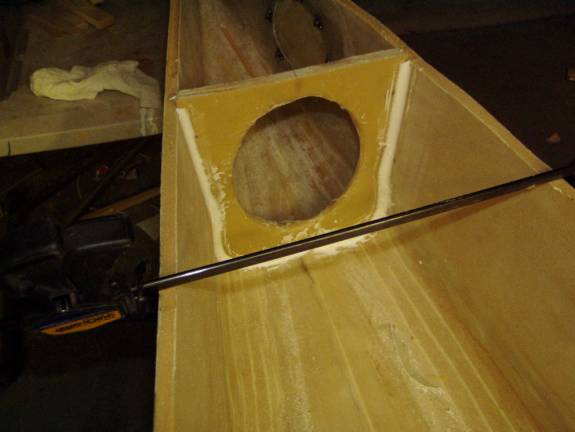
Thick Micro Radius and Fill Joint
Step 9 – Post Cure Fuselage interior – This is a good
time to post cure the fuselage as it is still a manageable size and
all interior bonds are complete. I performed this by simply
covering the fuselage with a sheet of 1” thick polystyrene
insulation board and heating the inside with a heat gun. A
thermometer was used to monitor the temperature.
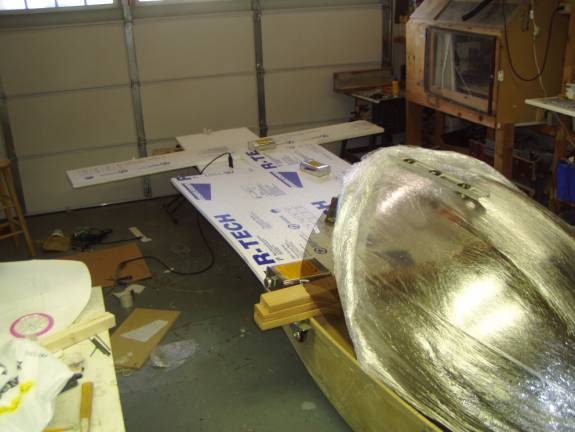
Post Cure the Rear Fuse Interior
|