Fuselage construction - Overview
The Super2 fuselage is constructed in several major sections. First,
the bottom half of the fuselage is built and is usually referred to as “the
boat”. It is built on a form, upside down. After the outside
is glassed, it is flipped over, the inside is glassed and bulkheads are
added. Then there is a turtle deck, which forms the rear top of
the fuselage behind the pilot’s head. The forward deck forms
the top of the fuselage in front of the pilot to the firewall. Finally
the canopy is built. Our first job is to fabricate the “Boat”.
The fuselage bottom is built on a form upside down. Prefabricated
panels are attached to this form and give it much of its rigidity. The
major panels consist of last-a-foam glassed on both sides. These
panels are fabricated on a flat surface, like a large work table or a
garage floor.
The soft lines of the Super2 are due to its radiused edges. These
radiused edges are created in two ways. The tailcone radius is
a flattened cone and is made by glassing the outside only of the ¼” thick
section of the tailcone panels. The section is then ‘folded’ into
the desired curve. The forward fuselage bottom corners are compound
curves and required a different technique. Even though they are
of a constant radius, the fuselage sides and bottom meet in a complex
curve moving through two planes. We will build this in a manner
similar to that used by a cooper making a wooden barrel. We use
multiple strips of ½”thick foam laid side by side
like staves in a barrel, then sand them from a hexagonal shape to a smooth
curved surface.
Our first job is to create all of the flat panels that will be used
to fabricate our “Boat”.
The panels that will be prefabricated are as follows:
- The forward side panels
- The forward bottom panel
- The four ½” thick foam sheets are cut for the tail cone
- The two ¼” thick foam sheets are cut for the tail cone
- The tail cone is assembled
Once the panels have been created we will build our form. We will screw
the three forward panels to the forms, the two sides and bottom, to create
a rigid structure. Then strips of ½” foam are temporarily
glued to the forms between the sides and bottom to form the radius between
the bottom and sides-our barrel staves. We will use a custom made
sanding tool to create a nice radius.
The tail cone has already been fabricated with the exception of glass
on the inside surface of the ¼” foam. This will allow
us to bend the tail cone into shape and secure it to our forms. We
glass the joints and the inside radius then flip the assembly over. We
install bulkheads and end up with a rigid fuselage bottom.
Panel Fabrication – Forward Fuselage Sides
Before we begin fabricating our panels, we need to understand the use
of joggles. We will join the panels together with fiberglass tape
in depressed areas at the edges of the panels called joggles. The
joggle depressions are made in our foam blanks by a simple sanding block. The
first panel made will be the forward fuselage side. It is the smallest
and simplest. Pull up the drawing for the forward fuselage side
and find the two datum axis.
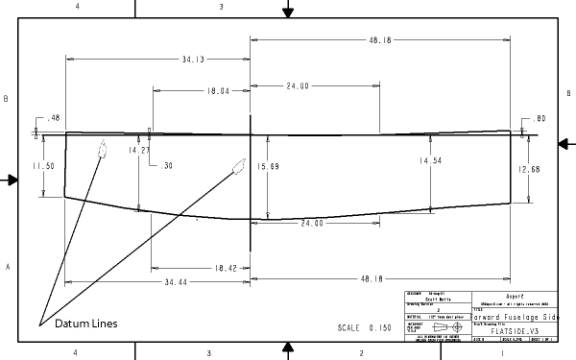
All of the dimensions on the drawing are referenced to these two datum
lines. Protect your garage floor with a large sheet of plastic drop cloth.
Start by laying out a 18” X 96 “ piece of 4.5 lb. Last-a-foam
on top. Go ahead and cut 6 inches off of the long edge of two pieces
of 24” X 96” last-a-foam to make the two side blanks. Lightly
mark the datum lines with a pencil using a laser level or a long straight
edge on one of the sheets. The lengthwise datum line should be drawn
about an inch from the top edge of the sheet. The vertical datum
line is drawn about 35” from the left edge of the panel. There
are ten points that define the shape of the fuselage side, 5 along the
top and 5 along the bottom. Using the dimensions shown in the drawing
mark these on the foam blank. Use small nails to mark these points—if
we use pencil, the points will be erased when we sand out joggles into
the foam. The top edge consists of three straight lines and the bottom
edge consists of a single smooth curve. Lightly mark the outside
edge with a pencil on the blank panel. The orientation of the
above drawing has the front of the aircraft is to the left, and the rear
to the right. Draw a second line 2” above the bottom curve. This
defines the upper edge of our joggle. Use a 2.5” X 2.5” square
block of wood with sandpaper affixed to lightly sand a joggle verhanging
.5” outside the bottom line. The joggle should only be about
1/16” deep. Use a small piece of 1/16” aluminum to lay into
the joggle to insure the proper depth. Fair the small edge of the joggle
trough with the top edge. Note" The pdf drawing looks like the fuselage sides are make of straight lines that do not correspond the the dimensioned locations. This is an aberation of the CAD program. Only use the points that are dimensioned.
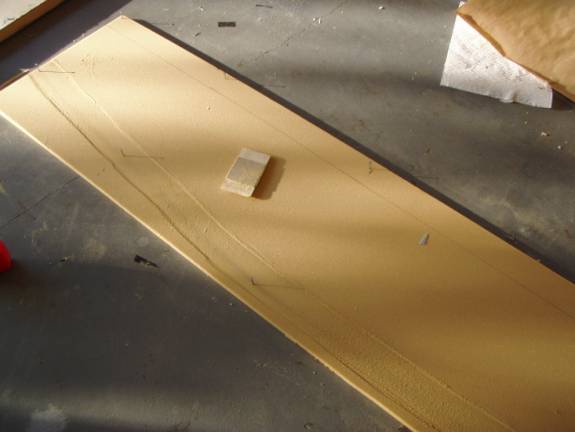
This photo shows the joggles sanded into the sheet of foam for a fuselage
side. A special joggle sanding tool is shown on the foam, it only
allows a joggle to be sanded a limited distance into the foam.
Repeat this process and create a joggle at the rear of the panel
and the top of the panel. A joggle is not required on the left
side (firewall side) of the panel. Align the first panel atop the
second panel and push the nails all the way through both panels. You
have now two identical panels. Use a pencil to mark the location
of the holes on both sides of both panels. These 10 holes will
fill with micro and need to be drilled out later. Set the second panel
aside and let us finish off the first. Get out your shop vac and
completely vacuum the sanding dust from the panel—it needs to be
absolutely dust free before we can slurry.
Measure out the cloth. We will use one layer of UNI and one layer of
BID on the outside and one layer of BID on the inside. Place the UNI
with the major glass strands running from the front of the aircraft to
the back (left to right in the drawing). If more than one piece of UNI
is required, the ends must have about a 2” overlap, but no overlap
is required if laid side to side. Measure out the BID for both
sides. The glass is laid out on the 45 degree bias front to back. All
BID sections must overlap by at least an inch. Mark the glass sections
and set aside. Use gallon size zip lock bags labeled with a sharpie
marker to hold the glass sections.
We are ready to perform the fiberglass layup. Be prepared to move
swiftly, but confidently. This is going to be our largest layup
to date. Pull all of your equipment together, mixing tools, squeegee,
brushes, gloves, cleaning supplies, etc. Slurry the entire foam panel
and lay out the UNI. Generously wet out with epoxy resin. Apply
the BID and wet it out with epoxy. Mix moderate batches of resin and work from the inside
of the panel outward. Use the squeegee to hurry the wetting out
process along. When the glass is fully wet and you are satisfied
with the way the glass lies and there are no air bubbles, use paper
towels to lift some of the excess resin from the panel. Wipe with the
major thread grops, from the inside of the panel to the edges (this would
be 45 degrees to the axis of the panel since we are using 45 degree bias
glass) Obtaining the proper amount of resin is a balancing act. Do
not dry areas so that the glass strands look dull and lift up, but do
not leave glossy pools of resin either. When you are satisfied
with the layup, you can lay peelply over the layup for a smoother surface. Again,
start in the middle of the panel and work your way to the edge. Multiple pieces of peel ply are easier to manage than one large sheet. When
satisfied, let the panel cure.
Congratulations, you have created your first fuselage panel layup. After
the panel is fully cured, peel off the large sheet of peel ply. It has been said before, but it is good to reiterate
here. Always remember to remove the peel ply, for if you do not
the joint will fail. Relocate the 10 datum points, drilling 1/16” holes
where the nail holes were marked on the back.
Flip the panel over and support the left and right edges about 3 inches
above the ground at each end—a 2X4 on edge works well. This
will approximate the curvature of the aircraft sides. Slurry and
glass with a single layer of BID on the 45 degree diagonal. Again
insure that you have at least one inch of overlap between pieces of BID. Let
cure. Use a saber saw or cut off wheel to cut the panel out along
the lines you made on the outside of the panel. Set aside.
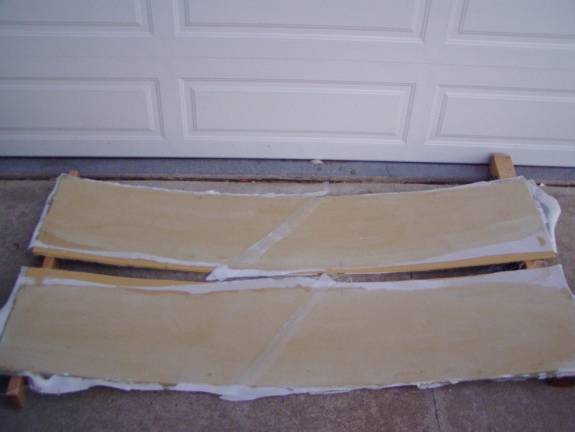
Now build a second fuselage side, but remember to build the opposite
side. If you build a pilot side the first go around, remember
to build a co-pilot side now.
Panel Fabrication – Forward Fuselage Bottom
The forward fuselage bottom is fabricated in a manner almost identical
to the fuselage sides. When you fabricated the fuselage sides you
used less than a full sheet of last-a-foam—you cut 6” off
to get a piece 18” wide. Take this 6” strip and attach
it to the long side of another piece of 24” X 96” last-a-foam. Use
a thick glass bubble mixture to bond the sheets together. Be careful
not to get too much squeeze out, this could cause a bump in our panel
later.
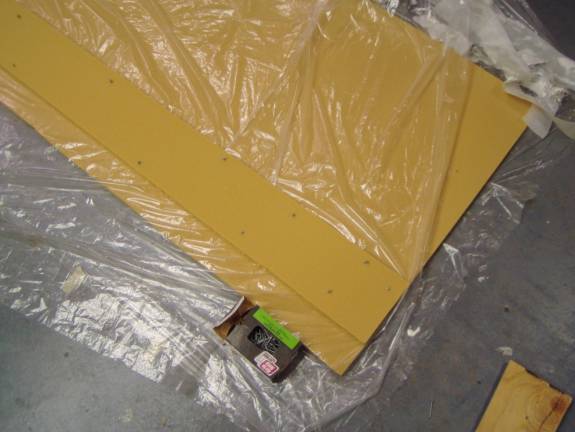
Layout the datum lines as we did before with the middle datum line going
right down the long axis of the panel. Locate and mark with small nails
the 10 points that define the shape of the bottom panel.
The
sides are continuous curves passing through these points on each side. Create
joggles in the long sides and the aft side of the panel as we did with the
fuselage sides.
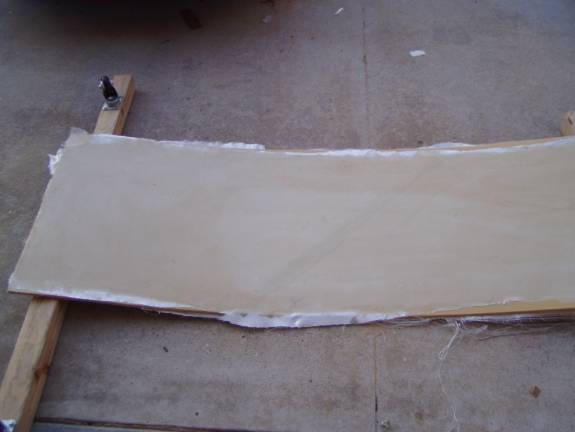
When glassing the inside of the panel, block up the ends 4” to
create the approximate curve of the fuselage bottom. Again, a 2X4 on
edge works well for this.
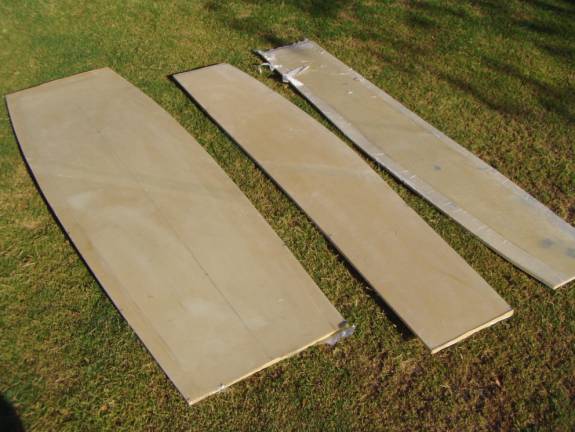
Congratulations, you have completed the three panels required for the forward
fuselage bottom. Now on to the tail cone.
|