Forward Deck
A small section of upper forward deck will be built behind the firewall. The
purpose of this top section of the fuselage is threefold—to
reinforce the firewall, to provide additional support to the engine
mounts and to support the forward edge of the windshield. Later,
foam sections will be fabricated that compete the forward top deck
around the edges of the forward canopy. These will be glassed
over and will contain the flange for the bottom edge of the windshield.
Print out three copies of the Firewall
Support Template and cut
them out and tape them together to create a template for ½ of
the firewall support bulkhead. The directions are on the printout.
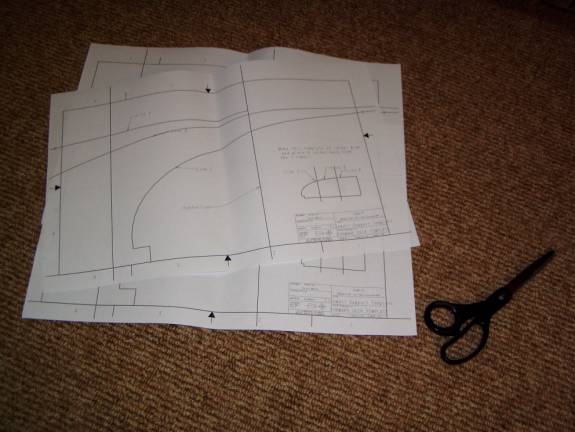
Cut one each sheet along line A, Line B and Line C. There
are vertical lines spaced 7 inches apart that are used to join the
three sections into one template. Tape them together
as shown in the little picture on the drawing. Use the template
to trace both halves of the firewall support bulkhead onto a piece
of ¼” thick last-a-foam.
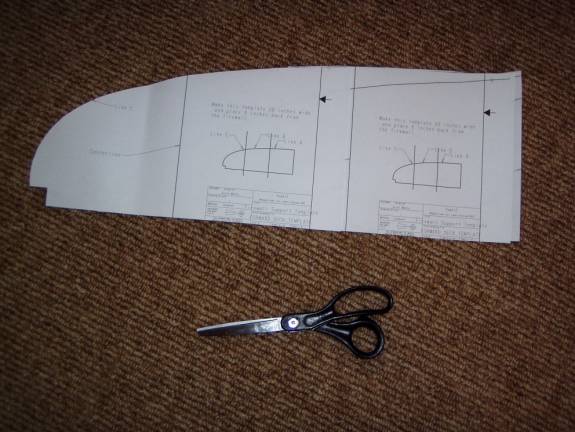
Cut a polygonal piece of ¼” last-a-foam 8” wide,
46” long on one side and 44” on the other. This
will be the top sheeting behind the firewall.
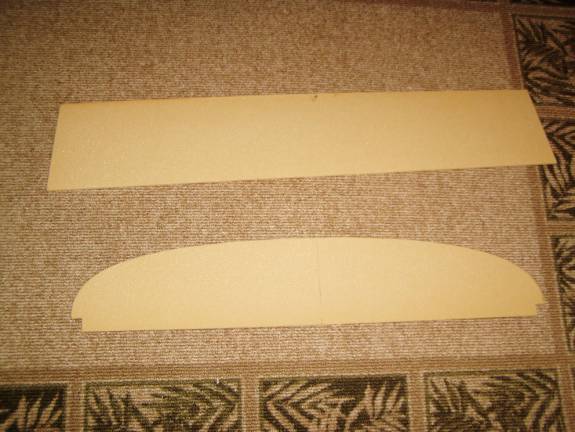
Level up the fuselage
Slurry and layup one layer of BID fiberglass on each side of
the firewall support bulkhead. Slurry and layup one layer
of BID on one side of the polygonal sheet, this will become
the top skin. Fill the edges of the firewall support
bulkhead with micro.
Sand a curve into the first 8 inches of the top inside edge of each
longeron right behind the firewall.
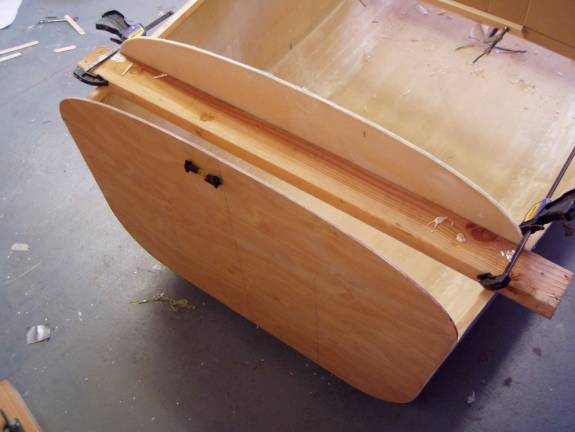
Use dabs of 5 minute epoxy and flox to secure the firewall support
bulkhead into position 8 inches behind the firewall. Use a
level to insure it is square. In the photo above, a 2X4 has
been used to insure the firewall support bulkhead is straigt and
true while the 5 minute epoxy cures.
The top sheeting is installed with the glassed side up. It
helps if the ends are pre-bent by working a curve into them by curling
over the edge of a small cylinder—I used a spray paint can. Gently
curve the ends to the general shape of the firewall and support bulkhead. Use
superglue and spray CA accelerator to tack the top skin in position
between the firewall and the support bulkhead. Mark the center of
the top skin and align it with the centerline marked on the firewall. Start
in the center and work outward to the two sides. Push the top skin
down between the firewall and support bulkhead and then spot glue
with CA (superglue). Hold until the glue is cured and then
workn further out until the entire panel is glued into position. Trim
the glass back to the top skin is equal to the top edge of the firewall,
support bulkhead and fuselage sides.
Mix a batch of thick micro. Fill any holes around the eges
of the top deck skin.
We now need to create a micro radius around the edges of the foam
side of the top skin. This is easiliest achieved if we flip
the fuselage onto its side. Slide a short 2X4 to support the
forward fuselage side, then sit on the inside of the fuselage side.

Fuelage on it side to allow access to inside of top forward deck
Look closely at the above phot and you can see a 2X4 sticking out
under the fuselage just under the lamp pole. This was used
to support the fuselage to allow one to sit insde the fuselage to
gain easy access to the inside of the top deck. A lamp was
used to light up the work area.
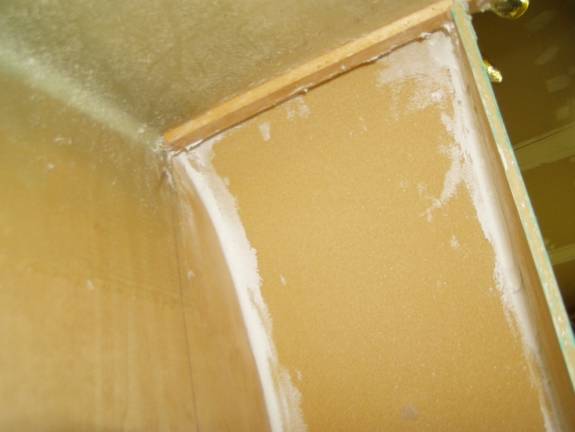
Micro around the edges of the top deck skin.
Use the thick micro to create a radius around the edges of the top
forward deck skin on the inside as shown above. Let this cure. Usually
we do not need to let our micro radis cure before we glass, but we
want to make sure the top skin is held solidly in place, and the
micro is the temporary adhesive until we glass the underside.
Cut three pieces of BID fiberglass to create a one layer BID layup
on the bottom side of the front deck.
Slurry the foam and layup a one layer BID over the bottom side of
the forward deck skin, overlapping about an inch and a half onto
the firewall, firewall support bulkhead and the two fuselage sides. The
BID should overhang the spruce longeron. This layup is easier
if done in the three pieces of BID as one long piece is difficult
to man handle in the awkward location.
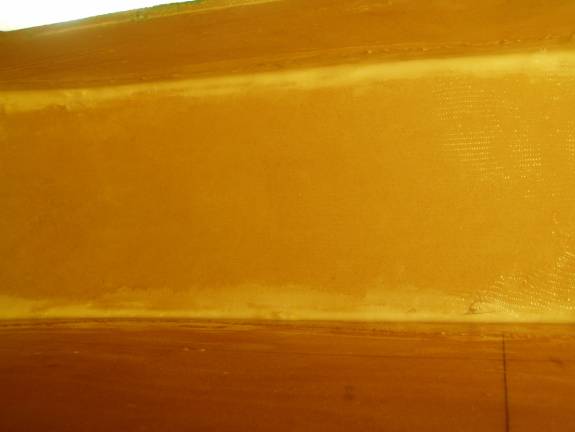
Completed single layer BID on underside of forward deck
Once the layup is complete, rotate the fuselage inverted and let
the resin cure. It is best to let the resin cure with the fuselage
upside down like this so the resin does not run.
Once cured, flip the fuselage right side up and cut strips of BID
three inches wide.
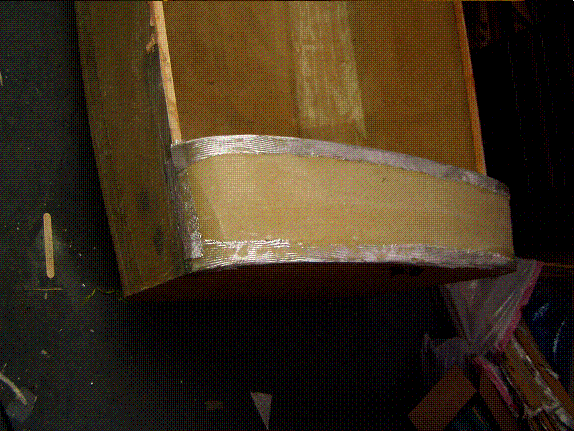
Fiberglass BID to seal edges of top deck skin
Layup one BID all around the edge of the front deck skin on the
outside as shown in the above photo. The Bid should overlap
onto the firewall, firewall support bulkhead and the fuselage sides
by at least and inch and a half.
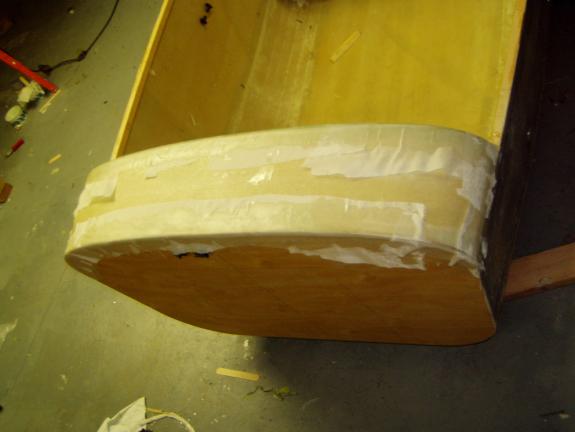
Cover the layup with strips of Peel Ply
Use multiple strips of peel ply to cover the layup as shown in the
above photo. Let cure.
|